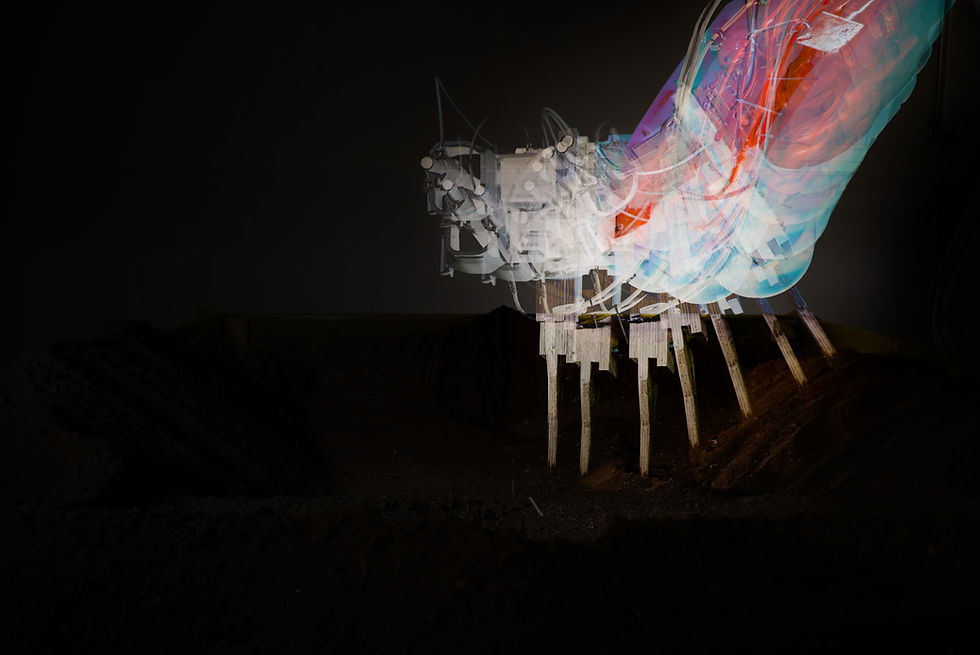
SHAPE-ENV
ENHANCED ROBOTIC TERRAIN-SHAPING FOR 3DCP
Project ID

PROJECT BY
PARTNERS
YEAR
SITE
TYPE
TEAM
ROLE
SDU.CREATE, Led by Assoc. Prof. Dr. Roberto Naboni
Hyperion Robotics, Weber Saint Gobain
2023
Odense, South Denmark
Research Project
Luca Breseghello, Ardeshir Talaei, Daniele Florenzano, Roberto Naboni
Researcher, Computational Designer
Project Description
SHAP-ENV aims at expanding the horizon of large scale additive construction by exploring the possibilities of conformal 3D Concrete Printing, 3D scanning and robotic terrain shaping with the goal of developing innovative digital workflows able to expand the design possibilties of large-scale 3D concrete printing.
This project addresses the environmental impact of the construction industry by envisioning a fabrication method that exploits the excavation soil of construction sites, which makes up a significant portion of construction waste and is usually sent to landfills.
Moreover, using unprocessed soil as a non-planar printing bed for on-site 3DCP, SHAP-ENV’s workflow envisions a multi-step process where a robotic arm performs terrain shaping and conformal extrusion, following a digital target model. To overcome the uncertainties arising in working with soil with variable composition and properties, we incorporate 3D scanning through depth cameras to guide the process.
This robotic fabrication method has been successfully tested in a lab environment through the development of a proof-of-concept bespoke doubly curved hollow shell panel. This approach provides a sustainable and cost-effective solution for large-scale 3D concrete printing using readily available soil resources, while enabling the possibility to exploit the benefits of automated construction in remote and unknown environments.

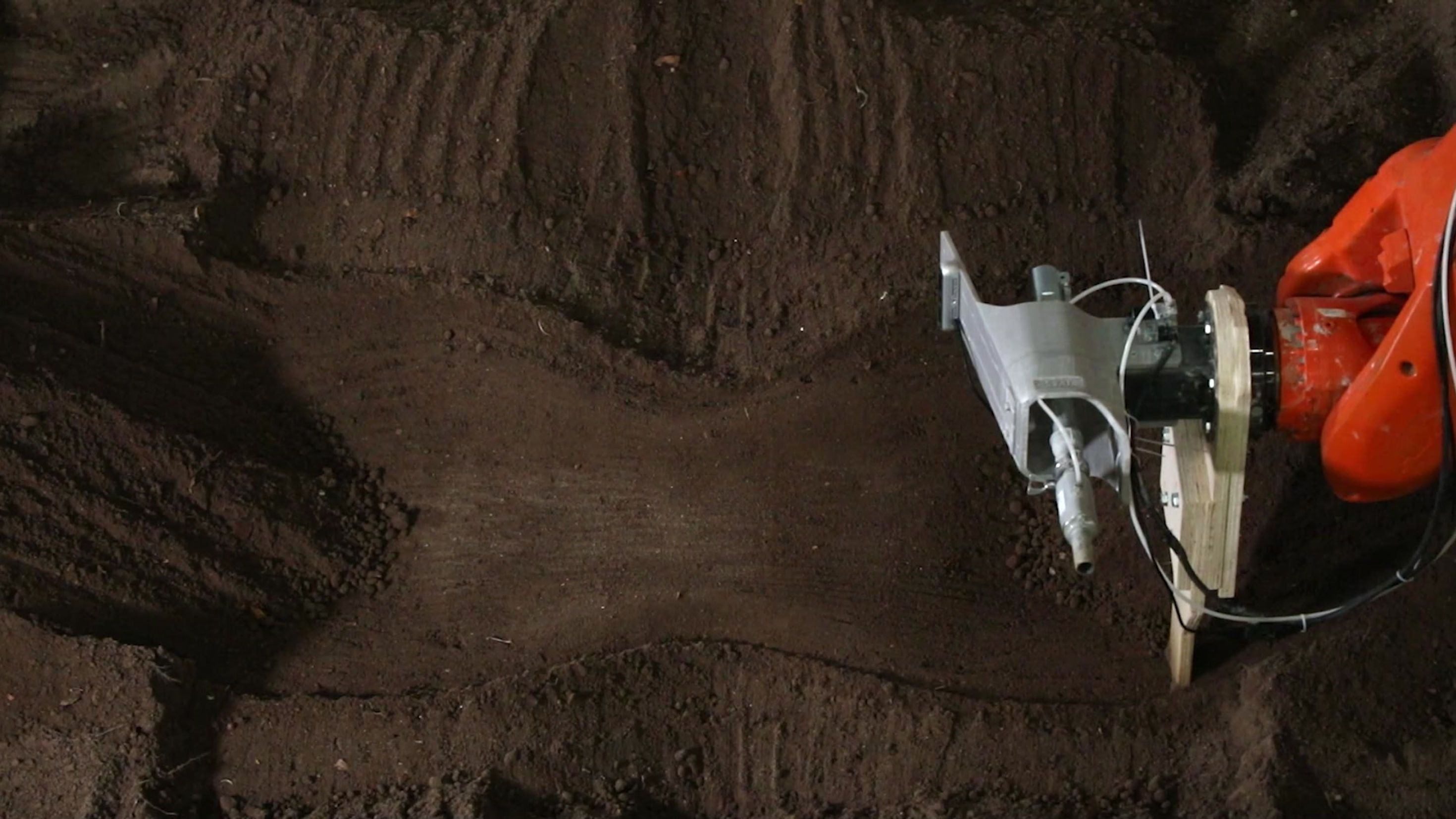
Multitasking End-Effector

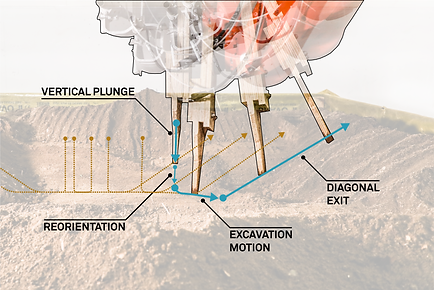
EXCAVATION MOTION
Discrete motions mapped onto desired surface composed by four distinct motions: vertically plunging into the terrain, reorientation of tool, excavation along path and diagonal exit.

PRINTING MOTION
The printing motion performed on the excavated supporting material requires control of the extruded layer width. This is achieved using a range of variable robot speeds.
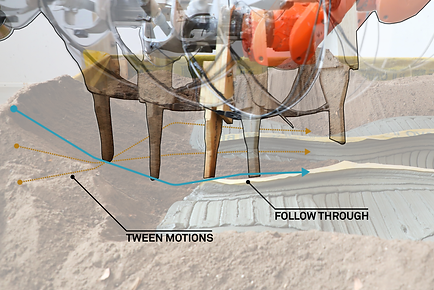
EMBANKMENT MOTION
This motion is composed by a twofold process. After scanning the resulting soil layout, a rough motion of the required volume of soil is executed, followed by a refinement motion.
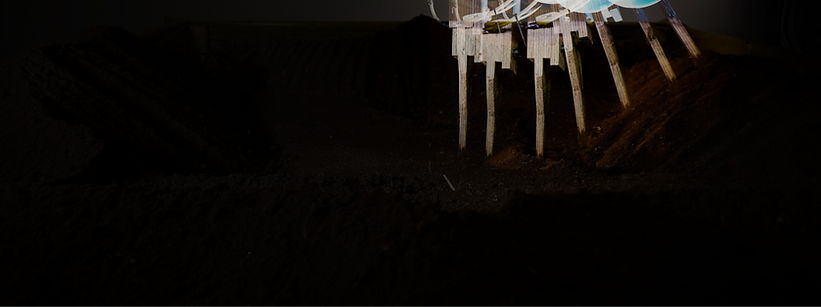